Why PLM is vital for your manufacturing company
In times characterized by increased digitalization and customer expectations, manufacturing companies are facing growing challenges. Customers demand faster delivery, lower prices, and higher quality in an intensely competitive market - and at the same time, products are becoming more complex. The integration of advanced software and electronics into traditional mechanical components has changed the rules of the game. This forces companies to optimize processes and streamline production to meet these expectations.
The largest challenges for manufacturing companies
We have asked our customers about some of their biggest challenges and they say, among other things:
- "The way we work is not optimal"
- "Our quality is not where it should be, if we produce incorrectly, there is a large amount of scrap that has to be thrown away"
- "Our lead times are too long"
How can PLM help and create value?
PLM is a system that, among other things, centralizes data from a number of data sources and supports many different types of data. It is through this centralization that value is created, as problems arise precisely on the basis of a silo-based structure in the organization.
The various silos could, for example, be quality planning, BOMs, configuration management, etc. Each silo contains data and, as we often see, is controlled in an Excel sheet, is dependent on data from other silos. Therefore, there should be coherence over relevant data, so that there is only one truth.
This is where data centralization comes in and plays an important role. PLM provides, among other things:
You can effectively manage the process of developing a product that contains several approval phases. If your engineering team comes up with a draft CAD model for the product, which is not approved either due to design issues or non-compliance with regulations, the model goes back to the design team, who come up with a new draft.
Here, PLM plays a large and decisive role by facilitating a structured feedback and audit trail that ensures effective communication and handling of changes.
product data
With the help of PLM, your company avoids silo structures by establishing an integrated platform where data is shared across relevant functions and processes. In a silo-based structure, you can e.g. not achieve digital traceability, which can be a direct requirement for the industry. By breaking these silos and creating a common platform for data sharing, you can achieve a more efficient and transparent operation.
This means that all data is collected in one place and not in silos, where data can easily be overlooked.
For example:
A given component in your manufacturing company can be included in several BOMs, e.g. BoM Commercial, BoM Engineering, BoM Manufacturing and BoM Service. If there is a change for this component, you traditionally have to manually update this change in all BOMs. If the data is not the same everywhere, mistakes and misunderstandings can occur later in e.g. the production process. Even with a single component, this coherence of data is difficult to achieve - and almost impossible when you have hundreds or thousands of components, which are also included in several BOMs or are included in several different end products. This is an overly complex management and updating of data.
PLM in collaboration with ERP
The ultimate collaboration between the development and production department happens when you have a PLM system that collaborates with your ERP. We believe that PLM is just as important as ERP, and that the interaction between these creates new opportunities for efficiency from development to production and puts you ahead of the competition.
After the webinar, 100% of the participants in the webinar were also of the same conviction. Watch the webinar on-demand here and see if you too will be convinced.
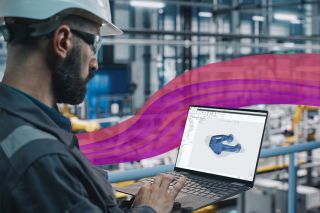
Conclusion
The integration of PLM and ERP represents a technological upgrade that puts your company ahead of your competitors. By bringing these systems together, the company can navigate complex product development landscapes, optimize supply chains and meet new, increasing demands from the market. This collaboration between PLM and ERP paves the way for more efficient workflows, reduces costs and improves product quality, which is essential for maintaining competitiveness. By doing this, your company not only ensures current success, but also ensures future growth and staying one step ahead of the competition.
Shall we have a talk about PLM?
Have a no-obligation chat with one of our experts about PLM and how it can create great value for your company. Fill in the form and we will contact you as soon as possible.