Increase internal efficiency and collaboration between engineering and production
Increasing internal efficiency and collaboration between the engineering and production departments is a priority at many manufacturing companies, but doesn't always prove easy in practice. Below you will discover why it is important to align these departments.
Do you recognize these challenges?
In the dynamic world of manufacturing companies, efficiency is key. Yet, many organizations face common challenges that can disrupt manufacturing processes. Do you recognize any of the following obstacles?
The Bill of Materials (BoM) that derives from the engineering department is not compatible for use in production. Therefore, a seamless translation into a Manufacturing Bill of Materials is critical. Unfortunately, this transformation still appears to be mostly done manually, often in Excel, leaving room for human error and inefficiency.
Often, product-related information is still decentralized within different departments, such as engineering and production. The lack of a single central source of truth creates an environment where manual errors, duplicates and tensions between engineering and production departments run free.
Is your engineering department facing challenges when it comes to effectively communicating component replacements across the entire organization? Clear and unified communication in this area is not always straightforward.
Even when the production department identifies issues—such as components that don’t fit—it remains a significant challenge to relay these problems accurately and efficiently to the engineering team, especially when there is no well-defined revision management process. In some instances, inadequate communication between the two departments results in engineering not promptly addressing feedback or becoming aware of specific issues until later. Consequently, production continues to encounter the same problems. Timely problem identification is crucial. The farther down the organizational chain changes need to be accommodated, the more costly it becomes for the company.
Within manufacturing companies, there are usually two engineering departments: one specializing in mechanical designs and the other handling electrical designs. This often results in the supply of separate Bills of Materials to the production department, which is more difficult to interpret than one Bill of Materials (where the two are combined). Some companies even work with three engineering designs: mechanical, electrical and electronics. These too, are ought to be delivered to production in one Bill of Materials.
A common struggle for companies is using the right, user-friendly tools to improve communication between engineering and production. In fact, not every tool is as user-friendly and easy to handle from the production department.
When the engineering department seeks to reutilize specific components from a prior project for a new initiative, this endeavor often presents significant challenges. Finding the right components can be a real quest, especially since they are scattered across different folders without a clear structure.
Often companies are left with unclear product drawings and/or instructions, making it not always obvious to assemble/make a product. Using 3D design can make this process easier.
Also, the new generations of designers entering the field are more familiar with working with 3D data.
Integrate your engineering and production departments
Do you recognize the above challenges? Then it is advisable to link your engineering and production departments.
By creating a digital common thread between the engineering and production departments, you ensure that communication and data flows seamlessly from engineering to production - and vice versa. Moreover, you create one single source of truth regarding product-related data, ensuring that everyone involved works with the same up-to-date information.
The more closely these departments are integrated, the faster and clearer information and changes flow from one department to another.
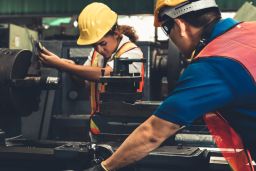
How to get started.
You should start by linking your CAD (Computer-Aided Design) and PLM (Product Lifecycle Management) solutions so that data from the CAD system can flow to PLM. In fact, PLM is responsible for managing all product-related data and keeps track of product revisions. It also handles the translation from the Engineering Bill of Materials (EBoM) to the Manufacturing Bill of Materials (MBoM), in conjunction with the ERP system.
How does racking manufacturer NEDCON use PTC Creo (CAD) and PTC Windchill (PLM)?
Given the complexity of their products, NEDCON was looking for an engineering solution that would help them encompass that complexity and ensure transparency and quality. They ultimately chose the PTC solutions CAD Creo Parametric combined with PLM Windchill.
The added value for your company
By linking your engineering and production department and letting data run via a digital common thread across your departments, you can realize significant benefits:
- Better collaboration between engineering and production
- Less manual input and reduced risk of errors
- Increased efficiency
- Increased employee motivation
- Cost savings
- Traceability
Need more information? Contact us! >