Improve your product quality with IIoT
Every self-respecting manufacturing company measures the quality of its delivered products. Fortunately, today that doesn't have to be so difficult. Using IIoT sensors, you can monitor the quality of your production line automatically and in real time. Do you want to improve your OEE in a relatively short period of time? Then IIoT is the ideal way to tackle this.
Product quality is an important part of the Overall Equipment Effectiveness (OEE) concept, the key measure of your company's productivity. In addition to the availability of your machines and their performance (e.g., the number of products delivered per unit of time), you also want to know to what extent your production line delivers good or bad products. Very specifically, by product quality we mean the percentage of products that make it through the entire production process without defects or additional adjustments.
Product quality losses can have a severe impact on your sales and profit margins. If you want to improve your OEE, you need insight into your production quality.
Quality loss at startup
Frequently, product quality degradation occurs following a production line restart or conversion. This loss is typically accounted for. It is common practice for a production line to operate for a specific duration until the machinery stabilizes or the parameters align correctly.
However, mitigating such quality loss is not always a straightforward process. Operators diligently fine-tune the machine settings prior to startup, yet even then, identifying the root cause of quality degradation can be challenging. Nevertheless, by integrating Industrial Internet of Things (IIoT) sensors into the machinery, it becomes feasible to detect patterns during each restart, expediting problem diagnosis. IIoT sensors present a superior alternative to the trial-and-error approach commonly used for parameter configuration during startup.
Quality loss during runtime
Even after the unstable startup of your machine, quality loss may still occur. Perhaps the operator misinterpreted instructions, or the machine was operated incorrectly, or certain components began to show wear.
Very often, poor product quality is an omen of a more serious machine downtime or impending failure. Of course, you don't have to wait for such downtime to intervene. Moreover, if a production line continues operating until its machines fail, the repercussions are frequently more significant than the mere loss of product quality. The breakdown can result in a long downtime and perhaps even pose safety risks to your staff. That's why it's so important to intervene in time, exactly something IIoT can help with.
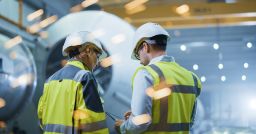
Process monitoring with IIoT
IIoT sensors can start measuring relevant parameters, such as temperature, speed or pressure, in real time. This prevents parameters from shifting and delivering poor quality. IIoT software can also help you detect trends or patterns in your processes. This allows you to see how or where poor quality occurs, and intervene in time with corrective measures. Without IIoT, it is often difficult or time-consuming to arrive at a conclusive root-cause analysis. Using data captured via IIoT sensors, it can be done faster and more efficiently.
Monitoring your production process and product quality with IIoT has another advantage. Often shifts in parameters (e.g., oven temperature) are so small and gradual that they are undetectable manually or with the naked eye. When parameters are measured digitally, the results are clear and unambiguous, facilitating the identification of specific patterns or trends in the production process.
Product quality monitoring with 9A Connected Factory & Insights
9A Connected Factory & Insights is an affordable IIoT platform that allows you to gain short-term insights into your production processes and product quality. You can use these insights to implement optimizations.
Clear dashboards give you all the necessary information about the performance of your machines and about your product quality. Moreover, you can set alarms when production errors threaten to occur, for example when certain threshold values are exceeded. This information allows you to optimize or intervene more quickly where necessary.
9A Connected Factory & Insights is a quick-start package based on PTC ThingWorx and developed based on best practices and industry knowledge. Our promise? After 90 days, you already have the first insights into your production process. So you'll get ROI from your IIoT project faster.
Interested in a demo of 9A Connected Factory & Insights? Let us know.